People, not applied sciences are the lacking hyperlink for manufacturing and supply-chain success.
For the manufacturing and provide chain sectors, the latest previous has been formative—and pre-COVID, this “formative latest previous” would have referred to the disruptive shift towards Business 4.0 applied sciences, together with the IoT (Web of Issues). Nevertheless, contemplating the pandemic, the formative latest previous should now embody all of the strife provide chains have confronted due to the fallout from COVID-19. Expertise is part of the image, however it’s removed from the entire image.
Provide chain executives have lengthy pursued extra visibility inside and management over provide chains. What COVID did was open everybody else’s eyes to the complicated, doubtlessly fragile nature of provide chains and simply how excessive the repercussions could be when these provide chains face huge and even reasonable disruption. In fact, it’s not simply COVID’s downstream results maintaining producers and provide chain executives up at night time. There’s financial uncertainty, cyber threats, labor and expertise shortages, and geopolitical pressure, for a begin.
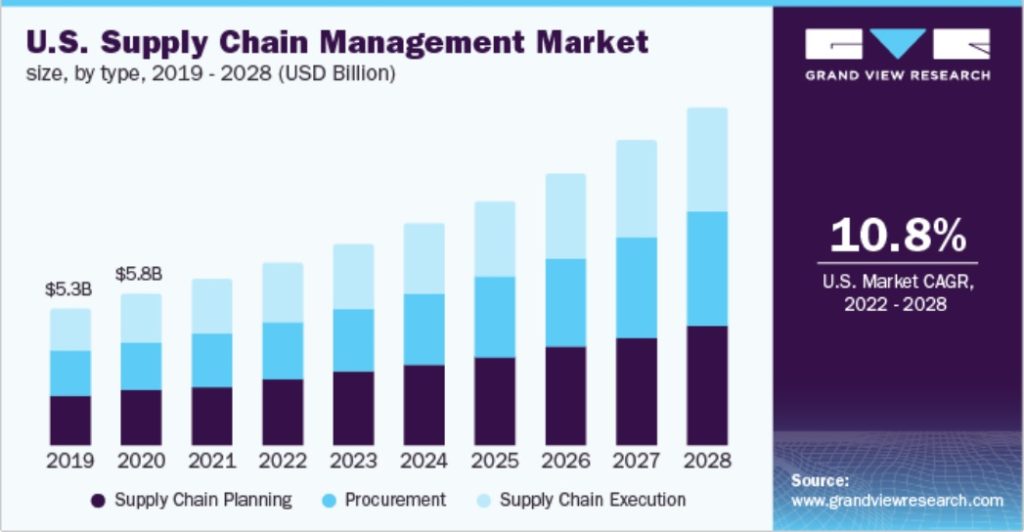
On the intense facet, the occasions from the previous few years have prompted long-term strategic initiatives aimed toward recovering, strengthening, and making ready provide chains for what might come subsequent. Many organizations are shifting their focus away from value and pace towards resilience—and that’s a great factor. Expertise and the acquisition of information—and, extra importantly, the flexibility to show this information into insights—is driving optimistic change. However what concerning the human part? Consultants say methods for stronger provide chains can’t depend on applied sciences alone.
What’s Going Incorrect?
Kind “provide chain points” in an online browser’s search bar and there’s all the time one thing new making headlines—from disruptions referring to Ford’s V8 engine manufacturing to delays on public transportation infrastructure initiatives and basic woes for U.S. meals retailers. These are the kinds of disruptions making information, however what number of different points exist behind the scenes? What’s actually maintaining producers and provide chain executives up at night time?
Nick Vyas, founding govt director of the USC Marshall Randall R. Kendrick International Provide Chain Institute and tutorial director of the USC Marshall Grasp of Science in International Provide Chain Administration, says growing market calls for, unprecedented cargo bottlenecks, labor shortages, service capability constraints, COVID-19, and geopolitical crises have made provide chains extra weak than ever. Vyas believes manufacturing executives are most anxious about one other world provide chain disruption. “With the rise of worldwide worth chains, delays within the manufacturing and distribution of supplies, elements, and merchandise are actually the norm,” he explains. “Due to the elevated demand, suppliers’ supply occasions in america and Europe, for instance, have reached new highs.”
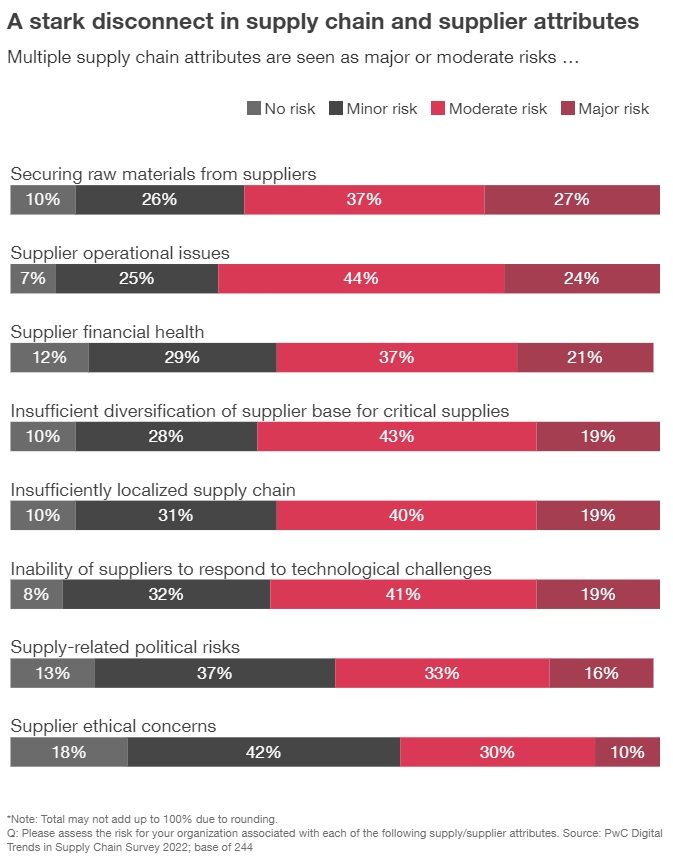
Cybersecurity and labor are additionally worrisome points. “Cyber threats are additionally a significant supply of concern, significantly ransomware and malware that may trigger tools and system sabotage,” provides Vyas. “Expertise acquisition, coaching, and retention are additionally vital constraints lately. The worldwide workforce is altering, and there’s a actual battle to draw youthful staff who’ve the potential mechanical and technical expertise. Producers should now take care of altering generational perceptions of labor.”
Financial uncertainty and geopolitical points are additionally entrance of thoughts for executives in manufacturing and provide chains. Vyas lists the deterioration of China-U.S. commerce relations and the Russia-Ukraine battle as examples of geopolitical points affecting these sectors. For Jeff Smith, professor and division chair for provide chain administration and analytics at Virginia Commonwealth College, what Vyas talked about and extra could be summed up in a single phrase: threat.
“By nature, many provide chain managers are inherently involved with guaranteeing techniques are practical. Due to this fact, the factor they fear about is ensuring duties get accomplished,” Smith says. “The issue is that threat is now spanning extra domains. Managers have to fret about provide availability, rising costs, digital transformation, inflation, world politics, market adjustments, information integrity, safety, and so on. Any of those facets might shortly disrupt the provision chain, so managers have to pay attention to how every might impression operations, and what s/he would want to do to offset any adverse ramifications.”
5 Issues Protecting Producers up at Evening
Bob Willig, govt director and CEO of SME, lists 5 issues maintaining manufacturing executives up at night time:
- Anticipating know-how adjustments and easy methods to pivot their enterprise shortly, permitting them to take care of competitiveness and profitability
- Availability of an impressed and expert workforce
- Uncooked materials availability
- Transportation/logistics complexity
- Capital availability and effectivity
Smith provides pre-COVID, many firms took the stance that if it was working, why mess with it? “Put up-COVID, many firms are exploring alternate provide configurations whereas setting up contingencies that account for potential disruptions,” he explains. “This might come at a value, nonetheless, because it means extra complexity from managing a larger variety of provide bases, whereas additionally doubtlessly having suppliers that reside in higher-cost elements of the world. COVID, albeit a horrible factor, did open managers’ eyes to the necessity to have a extra full understanding of the scope and scale of the provision chain in order to extra successfully handle the dangers that include the complexity.”
In different phrases, due to what they’ve skilled up to now few years, firms usually are not ready for an issue to plan for one. An necessary a part of that planning is know-how implementation.
Resiliency and Transparency by Tech
Cristina Farris, manufacturing and automotive advertising and marketing lead at Microsoft, says in the course of the previous few years, provide chain resiliency has come into the highlight for a lot of organizations, and producers are below stress to forestall and reduce disruptions to their operations. She says they’re seeking to spend money on methods that may make their provide chains extra resilient. “A technique that producers are seeing optimistic impression to the resilience of their provide chain is by adopting an industry-specific cloud platform that connects workflows, processes, folks, and property extra securely, making operations extra adaptable and offering visibility into realtime data that means that you can make adjustments within the second,” Farris says.
To producers seeking to leverage know-how to make their provide chains stronger, she says: “Contemplate a platform that unifies information from many sources and makes it digestible in realtime so selections are simpler and within the second.” Farris additionally advises firms search for options that enhance collaboration and belief. “For the provision chain to maneuver easily, it’s necessary to repeatedly hold companions knowledgeable and share provide chain information in a safe community that enables for collaboration on potential points and options,” she explains.
Farris additional suggests producers create digital twins of their provide chains, full with mannequin eventualities and simulations to anticipate issues. “Doing so permits organizations to automate the perfect response prematurely, saving time when disruption does occur. For instance, the flexibility to forestall sudden tools downtime utilizing combined actuality and the IoT to do proactive tools upkeep,” she says.
Christopher Tang, professor and chair in enterprise administration at UCLA, senior affiliate dean of worldwide initiatives on the UCLA Anderson College, and college director of the UCLA Heart for International Administration, says COVID has helped propel the adoption of Business 4.0 applied sciences, together with automation. Two trending applied sciences he mentions specifically are digital twins and blockchain.
“Blockchain can facilitate observe and hint to enhance provide chain transparency. This will scale back counterfeit and product adulteration,” Tang says. “Walmart adopted blockchain with 9 main distributors. IBM-Maersk developed a blockchain platform TradeLens to streamline the ocean freight processes to cut back the time to processing paperwork sequentially. Blockchain can assist to trace and hint carbon emissions, compelled labors, counterfeits, and so on., so it could possibly assist corporations to enhance their ESG (environmental, social, and governance) efficiency.”
Whereas bettering visibility and transparency was on the agenda for provide chain executives lengthy earlier than COVID and the present provide chain struggles, occasions and realities from the latest previous have made it clear how essential flexibility and agility could be. Flexibility and agility are greatest achieved with the assistance of visibility and transparency, which applied sciences like cloud, digital twins, blockchain, and extra can assist accomplish.
The Lacking Hyperlink
Ask Chris Caplice, senior analysis scientist and govt director of the CTL (Heart for Transportation and Logistics) at MIT (Massachusetts Institute of Expertise) and chief scientist at DAT Freight & Analytics, about what’s occurring proper now in provide chain, and he’ll say what the {industry} wants to speak extra about is the human part. “We spend a number of time targeted on all these applied sciences and we miss the human interface,” he says. “None of those can occur with out the human being concerned both within the testing of it, the coaching of it, or the precise utilization of it, a lot much less the upkeep of it. They’re all actually attention-grabbing applied sciences, however what’s actually lacking is the way it’s going to interface with people who really make selections. Machine studying doesn’t make selections, folks do. All of this stuff improve a human’s skill to make selections.”
Caplice says if worker coaching doesn’t sustain with know-how adoption, it’s not precisely a recipe for achievement. “The very best factor you are able to do to enhance any of those applied sciences is to upskill your present workers,” he says. “There’s an idea that’s known as the adjoining potential. The entire thought is that new innovation can’t be that far forward. What’s the one step over that we might do to make the method be higher, somewhat than two or three (steps forward), as a result of the implementation of that may be very lengthy and onerous and normally goes to failure.”
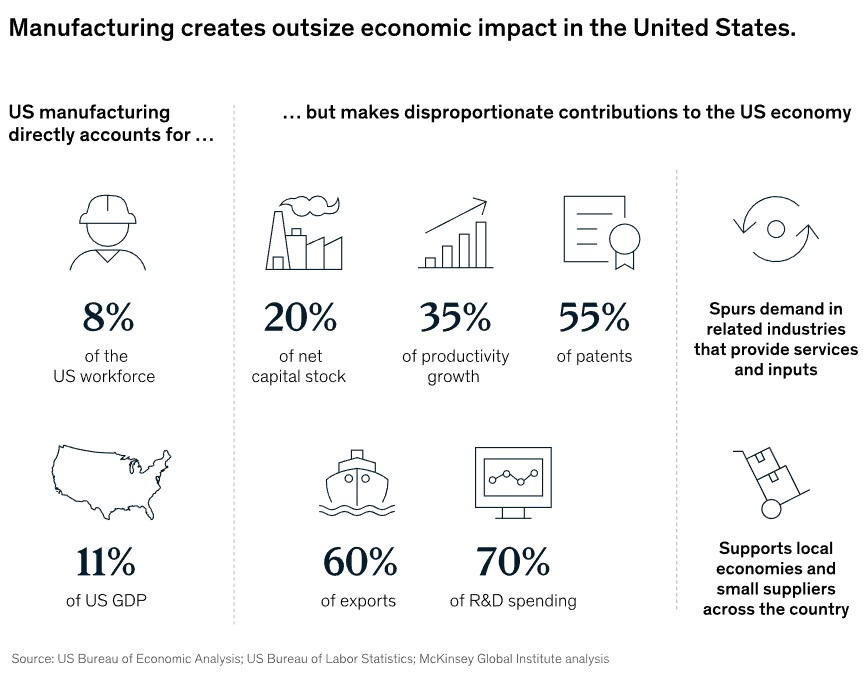
Upskilling can be necessary for worker retention. “One thing you are able to do to essentially assist retain somebody is to extend their expertise,” Caplice provides. “You possibly can’t simply change dock staff with automation and anticipate every little thing to go superb. You possibly can’t simply dump in a digital twin and anticipate somebody who was operating spreadsheets to know it instantly. So, understanding and getting the tradition to maneuver together with the abilities is a large problem that only a few firms are occupied with and are spending time on. (Folks) are the lacking piece of the puzzle at this level (and) it must be extra than simply having a random lunch for them to return in. It’s giving them onerous expertise.”
Joris Peels, vp of consulting at SmarTech Evaluation and govt editor of 3DPrint.com, equally suggests producers and provide chain executives should guarantee their workforce is educated and properly ready for the know-how adjustments of the long run. “A expertise hole is limiting the expansion of trusted workers’ rise from the concrete flooring to the assembly rooms of administration,” Peels says. “The shortage of upward mobility in firms is divorcing administration and company from what is occurring in manufacturing day-to-day. There’s additionally a expertise hole that’s making it onerous for firms to search out software program, CAD, engineers, and all types of those that they want. Inflation is spooking workers to demand larger wages or search for higher-wage positions as a result of persistence can result in penury now. That coupled with a good labor market implies that there usually are not sufficient staff. However what is simply too usually missed is, even when there have been sufficient, these staff don’t have the fitting coaching and expertise to optimally help and develop within the enterprise. There’s a complete mismatch between the kind of folks which can be wanted within the trendy manufacturing unit and the kind of folks which can be accessible to it. Corporations must do extra to coach their workers and to coach potential workers.”
Like Caplice’s adjoining potential argument, Peels says tech options can’t be pushed upon a workforce too shortly. “Typically, that is an uncomfortable time with operations folks having a really skeptical angle in the direction of a lot of the brand new software program tooling—and with good motive,” Peels explains. “Lots of the software program, digital twin, AI (synthetic intelligence), VR (digital actuality) stuff we see popping out now isn’t prepared for prime time and is being pushed far too enthusiastically by salespeople. Individuals are grappling with waste, emissions discount, a discount in vitality utilization, and far more, and software program and sensors are being seen as the way in which to attain this. However a number of the instruments being offered into the house are ridiculously ill-suited to be used on the manufacturing unit flooring. My favourite instance of that is touchscreen interfaces which can be cumbersome and never suitable with the protection gloves that employees need to put on.”
Microsoft’s Farris provides many manufacturing organizations are confronted with an growing old workforce—a so-called “silver tsunami” of retirements. “When these workers depart the workforce, they take their expertise with them,” Farris warns. “Not solely are producers shedding high expertise, however they’re additionally struggling to draw and retain new expertise. To maintain operations transferring, producers must reskill and upskill their present workforce and proceed to help their frontline staff.”
One of many methods organizations can do that is by utilizing know-how. “Expertise can empower frontline staff with digital instruments and trendy gadgets, permitting them to be extra productive and work from anyplace because the enterprise permits. Moreover, know-how can assist help with reskilling and upskilling for workers by offering entry to studying options, data and insights, and use-case eventualities. Producers who undertake and make the most of know-how that permits their folks and groups to be extra productive and collaborative will see larger success over the subsequent few years.”
Among the many methods for stronger provide chains, together with leveraging know-how to spice up visibility, transparency, and resilience inside provide chains shall be to by no means lose sight of the folks answerable for implementing these applied sciences. Coaching and upskilling staff at a fee suitable with know-how adoption will assist organizations inside manufacturing and provide chain study from the previous and put together for the long run.
Hyperlinks For Additional Studying:
Need to tweet about this text? Use hashtags #IoT #sustainability #AI #5G #cloud #edge #digitaltransformation #machinelearning #futureofwork #bigdata #blockchain #cybersecurity #smartfactories #manufacturing #supplychain #COVID19 #skillsgap #digitaltwin #upskilling #reskilling #ESG #Microsoft #SmarTech