Cement hides in plain sight—it’s used to construct all the pieces from roads and buildings to dams and basement flooring. However there’s a local weather menace lurking in these ubiquitous grey slabs. Cement manufacturing accounts for greater than 7% of world carbon dioxide emissions—greater than sectors like aviation, delivery, or landfills.
People have been making cement, in a single type or one other, for hundreds of years. Historical Romans used volcanic ash, crushed lime, and seawater to construct the aqueducts and iconic buildings just like the Pantheon. The trendy model of hydraulic cement—the type that hardens when blended with water and allowed to dry—dates again to the early nineteenth century. Derived from broadly accessible supplies, it’s low-cost and straightforward to make. At present, cement is among the most-used supplies on the planet, with about 4 billion metric tons produced yearly.
Industrial-scale cement is a multifaceted local weather conundrum. Making it’s power intensive: the within of a conventional cement kiln is hotter than lava in an erupting volcano. Reaching these temperatures usually requires burning fossil fuels like coal. There’s additionally a selected set of chemical reactions wanted to show crushed-up minerals into cement—and people reactions launch carbon dioxide, the commonest greenhouse gasoline within the ambiance.
One resolution to this local weather disaster could be coursing by the pipes at Elegant Techniques. Based by two MIT battery scientists, the startup is creating a completely new approach to make cement. As an alternative of heating crushed-up rocks in lava-hot kilns, Elegant’s know-how zaps them in water with electrical energy, kicking off chemical reactions that type the primary substances in its cement.
Elegant silicates (high dish) and lime (backside dish) are the 2 major reactive parts for making Elegant Cement.
Over the course of the previous a number of years, the startup has gone from making batches of cement that would match within the palm of your hand to beginning up a pilot facility that may produce round 100 tons every year. Whereas it’s nonetheless tiny in contrast with conventional cement vegetation, which may churn out 1,000,000 tons or extra yearly, the pilot line represents the primary essential step to proving that electrochemistry can stand as much as the problem of manufacturing one of many world’s most vital constructing supplies.
By the top of the last decade, Elegant plans to have a full-scale manufacturing facility up and working that’s able to producing 1,000,000 tons of fabric every year. However conventional large-scale cement vegetation can value over a billion {dollars} to construct and outfit. Competing with established business gamers would require Elegant to scale quick whereas elevating the extra funding it might want to help that progress. The tip of 0% rates of interest makes such a job more and more tough for any enterprise, however particularly for one producing a commodity like cement. And in a high-stakes, low-margin business like development, Elegant might want to persuade builders to make use of its materials within the first place.
The cement business pumps 2.6 billion metric tons of carbon dioxide into the ambiance yearly. Cleansing that up would require addressing the 2 distinct sources of cement’s greenhouse-gas emissions: warmth and chemistry.
To make cement at this time, a mix typically containing limestone, sand, and clay is floor up and baked in kilns at temperatures of as much as 1,500 °C (simply over 2,700 °F). The warmth kicks off reactions, reworking limestone to lime and mixing that with silicon dioxide within the sand and clay. These reactions are advanced, however normally the essential last product is a mix of some silicon, calcium, and oxygen compounds that permit the cement, after it’s blended with water (and sand and gravel are added), to harden into concrete, a sturdy constructing materials.
People use extra concrete, by weight, than some other materials besides water. Cement is the glue that holds that materials collectively, accounting for about 10% of its quantity.
Roughly 40% of the greenhouse-gas emissions related to cement manufacturing come from fossil fuels that generate the warmth required. It is a frequent downside throughout heavy business: fossil fuels have change into ingrained in manufacturing processes due to their low value, says Rebecca Dell, head of the business group on the nonprofit analysis group ClimateWorks. Nonetheless, lower-cost renewables are coming to the grid, opening the door for extra industrial sectors to modify to electrical energy.
It’s potential to make use of electrical kilns to make cement, and a few main business gamers, like Cemex, are working to pilot the know-how to chop emissions from warmth demand. These electrical kilns, if powered by renewable electrical energy, might present a possible pathway to chopping cement’s local weather impacts.
However that does nothing to treatment the opposite sources of emissions from cement manufacturing: the roughly 60% that come not from warmth however from the chemical reactions required to rework the beginning supplies into the constructing materials.
Most cement begins with limestone, a sedimentary rock that accommodates calcium, oxygen, and carbon. In cement kilns, limestone is changed into lime via reactions that peel away carbon dioxide, which is normally launched into the ambiance. Limestone is about half carbon dioxide by mass, so these emissions can add up. Meaning totally decarbonizing the cement business may require a extra radical reinvention. That is the place Elegant is available in.
“Cement doesn’t actually get the pizzazz that I believe it deserves,” says Leah Ellis, Elegant’s cofounder and CEO. She speaks shortly, as if working quick on time, ideas pouring out and conveyed with a slight Canadian accent. As she explains the intricacies of cement chemistry, her eyes shine behind bubblegum-pink glasses.
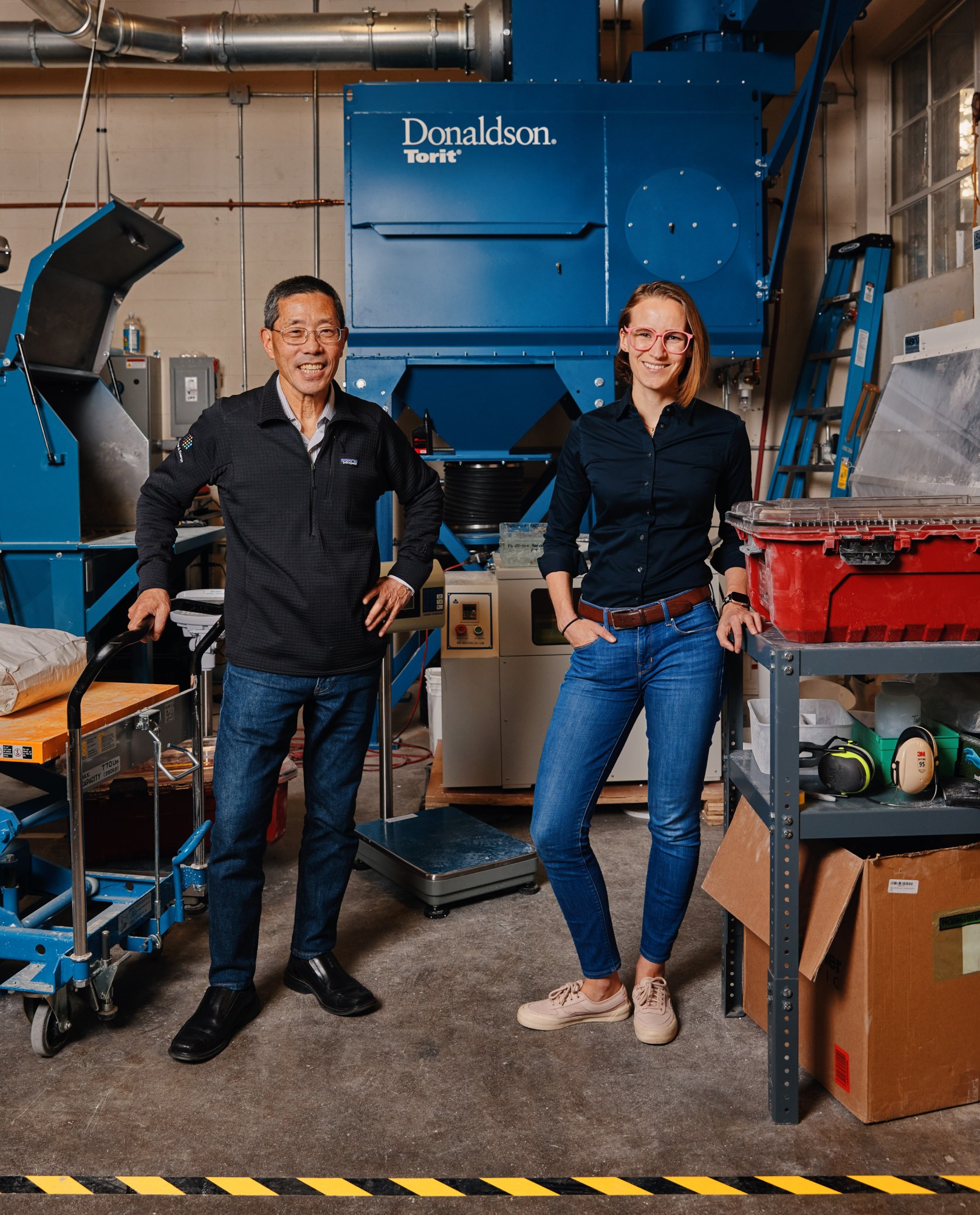
Ellis didn’t at all times plan on entering into the constructing supplies enterprise. After rising up in Canada, she accomplished her graduate work beneath the famed battery pioneer Jeff Dahn. She then struck out for MIT to work with But-Ming Chiang, one other main determine in battery analysis and a serial entrepreneur. Chiang has based a number of power storage ventures, together with A123 Techniques, 24M, and Kind Power, and is now a cofounder of Elegant Techniques with Ellis.
When Ellis first arrived at MIT, it was Chiang who floated a special concept for her potential analysis there. She recollects him ushering her into his workplace and, to her shock, asking if she was uninterested in batteries. “And I assumed it was a trick query,” she says, “as a result of he’s clearly a well-known battery scientist.” However Chiang had an concept for making cement in a brand new approach, utilizing a software from the battery-science software package: electrochemistry.
At full capability, the pilot line would take per week to make sufficient cement to produce a single concrete truck.
As an alternative of burning fossil fuels to warmth up cement kilns, Chiang urged, there could be a approach to spark the mandatory chemical reactions to make cement utilizing electrical energy.
The crew later found {that a} machine known as an electrolyzer could be helpful in such a course of. Electrolyzers are gadgets that use electrical energy to kick off chemical reactions. They’re normally used to separate water into its parts, producing hydrogen and oxygen. However electrolyzers can work with different chemical reactions too, like producing acids and bases—the potential key to a brand new cement manufacturing course of.
By 2019, Ellis and her fellow researchers had found a technique with potential to satisfy Chiang’s preliminary concept. They discovered that an electrolyzer might be used to type a pH gradient in a tank, with dissolved limestone on the acidic finish and hydrated lime on the opposite. That lime might then be mixed with reactive silica to type the identical compounds shaped by conventional cement.
After some extra technical improvement and business evaluation, the pair determined to spin out the analysis into an organization with Ellis on the helm. Chiang says, “It didn’t take very lengthy earlier than I acknowledged that there was each a beginning concept and likewise an individual to hold it.”
A Elegant worker removes the corporate’s reactive silica product from its gear as a part of an R&D-scale manufacturing course of.
A Elegant worker checks the compressive power of the corporate’s cement in concrete cylinders.
4 years later, Elegant is working a pilot manufacturing line. It’s a significant step up from the early days at MIT, the place Ellis and her lab mates would produce about sufficient materials to make a single die. The road began up in late 2022, says Mike Corbett, Elegant’s director of engineering, and is 20 instances bigger than something the corporate had run within the lab.
Inside a cavernous room on the startup’s headquarters, the stainless steel tanks lining the partitions of the pilot area are organized roughly from left to proper. Into tanks on one aspect of the room go ground-up rocks, and out of these on the opposite comes hydrated lime, one of many major substances in Elegant’s cement.
The outcomes of varied experiments and trial runs sit close by, in five-gallon buckets stacked on steel racks. When Corbett and a colleague crack the lid on one, the hydrated lime inside is an unassuming white powder, chalky and barely clumped collectively like baking soda in a field that’s been left open for too lengthy.
It will be tough to make use of what’s in these buckets to construct something: at full capability, the pilot line would take a couple of week to make sufficient cement to produce a single concrete truck. And it takes three to 4 truckloads of cement to pour the inspiration for only one common single-family residence within the US.
As an alternative, the startup is making materials to ship to potential companions, working checks on cement blocks, and, crucially, serving to design the following amenities. These, which will probably be considerably bigger, might be the ultimate step in proving that Elegant’s course of can work within the cement business.
Elegant Techniques isn’t the one participant making an attempt to inexperienced up the grey glue. Early efforts to chop emissions from cement have largely targeted on effectivity, says Radhika Lalit, the initiative director for business on the Local weather Crucial Basis, who previously labored within the business group on the Rocky Mountain Institute, a nonprofit analysis company. For instance, including fillers known as supplementary cementitious supplies, which may react with the lively substances in cement, might help reduce down on complete emissions with out affecting the properties of the concrete.
This technique solely works as much as a sure level, Lalit factors out: after that, these fillers will start to degrade the power and lifelong of cement.
There are different methods so as to add supplies to cement to chop local weather impacts. The Canadian firm CarbonCure Applied sciences, for instance, has developed know-how to inject carbon dioxide into cement mixtures. In accordance with CarbonCure, the gasoline can then react with the combination and mineralize, locking it away from the ambiance and including to the fabric’s power. CarbonCure is working with carbon elimination corporations like Heirloom Carbon Applied sciences to reveal the potential for utilizing concrete for long-term carbon dioxide storage.
However strategies like chopping down the entire materials used or including in fillers are restricted in how a lot they will reduce emissions: it’s not potential to make limitless effectivity tweaks to get to zero. So many established gamers within the cement world need to add carbon seize and sequestration vegetation to current amenities, Lalit says. By snaring carbon dioxide from plant exhaust earlier than it may be launched into the ambiance, this add-on helps lively amenities reduce their emissions in order that making the business cleaner doesn’t require changing them totally.
Including carbon seize know-how to current infrastructure might imply an extended lifetime for standard gear, a significant profit for just lately constructed vegetation which can be typically designed to run for 30 to 50 years. However carbon seize continues to be largely unproven in heavy business: current strategies typically aren’t in a position to seize all emissions, and the few current large-scale models have confronted delays, Lalit says.
To be on monitor for net-zero objectives, the cement business would want so as to add carbon seize amenities to between 33 and 45 current cement vegetation by 2030, in response to RMI. The primary such industrial-scale facility at a cement plant is scheduled to return on-line this 12 months.
This might be costly: a carbon seize system might value as a lot as $120 per metric ton of carbon dioxide eliminated, which Ellis says would roughly double the ultimate value of cement at present costs.
The price is one purpose Elegant and a lot of different startups are eschewing carbon seize and aiming to chop cement’s carbon footprint utilizing extra radical formulation.
One of many different best-funded cement startups is Brimstone, a California-based group with what it calls a carbon-negative course of for making cement. Which means the product finally ends up pulling extra carbon dioxide out of the ambiance than it emits, says Cody Finke, Brimstone’s CEO.
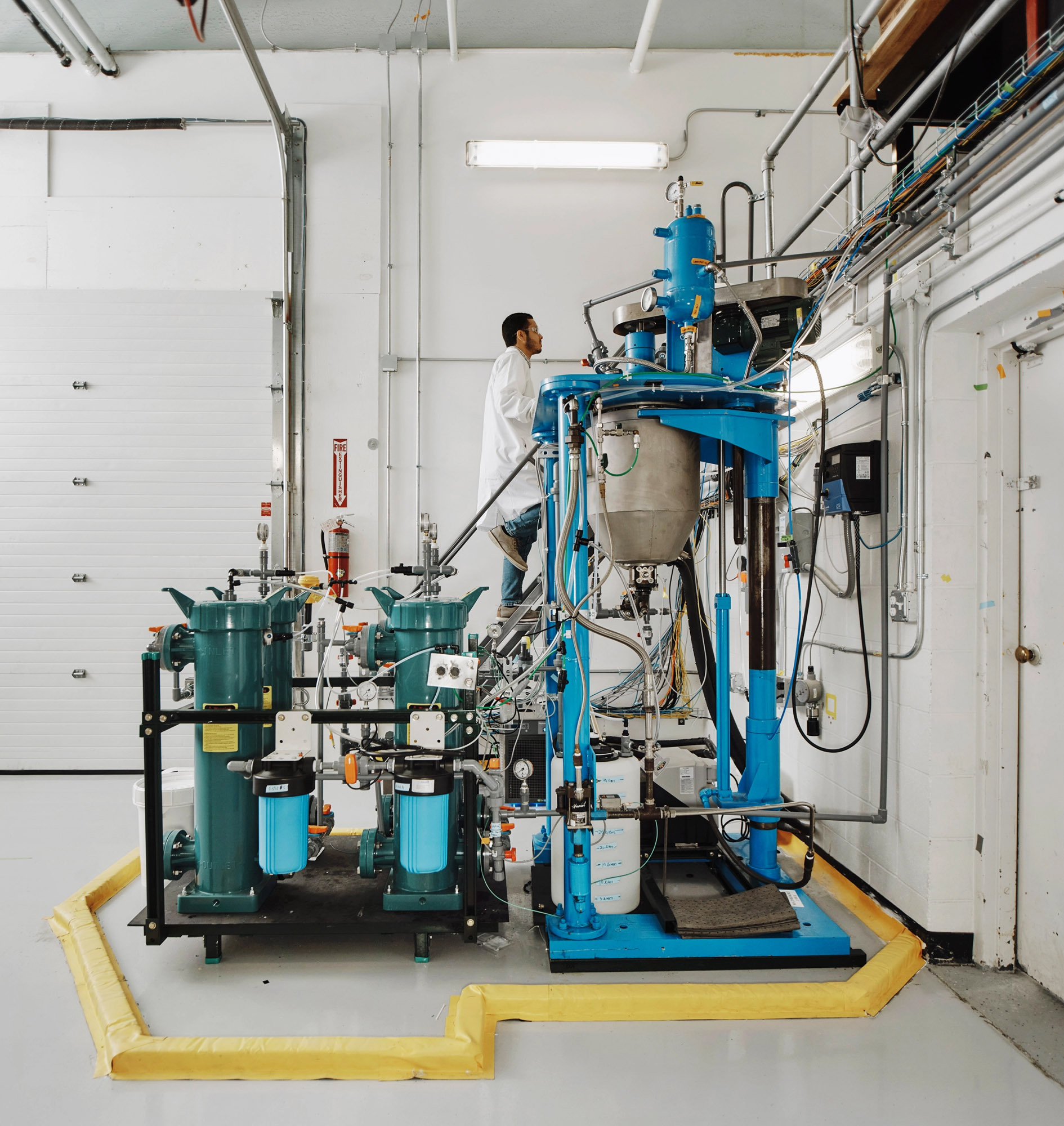
engaged on designing its subsequent amenities, which could have even better capability.
This works in two main methods. First, quite than limestone, Brimstone makes use of different minerals known as silicates that don’t include carbon dioxide, so there aren’t any course of emissions from the corporate’s cement, says Finke. As well as, a waste product of the silicates is a magnesium-containing materials that acts like a sponge, absorbing carbon dioxide from the air and mineralizing it.
There are nonetheless emissions related to making Brimstone’s cement, largely associated to the warmth required. However they are often successfully canceled out with the mineral course of, Finke explains, particularly for the reason that firm plans to make use of electrical kilns. If these are powered by electrical energy from the common US energy grid, the startup claims, its materials would wind up eradicating extra carbon dioxide than it produces—about 130 kilograms extra per ton of cement.
The explanation Brimstone is sticking to this high-temperature course of, regardless of its related power wants and emissions, is that it’s producing a cement with a chemical system that dominates the business at this time. Portland cement, which has been round for the reason that early 1800s, is probably going what you consider if you consider cement. It’s identified for producing predictable and powerful concrete. Nonetheless, there’s a catch: making it necessitates ultra-high warmth, as a result of a key ingredient of the cement—alite—can solely type at temperatures over 1,250 °C.
“A cement startup might be one of the tough ones you’ll be able to think about. Not solely is it technically tough, however it’s very capital intensive … And it’s not attractive.”
Leah Ellis, Elegant’s cofounder and CEO
Initially, Elegant deliberate to make Portland cement as nicely. “For one thing as low-cost as cement, we thought you’d want to provide what the market is used to utilizing,” Chiang says. However the temperature necessities pushed Elegant to rethink because it started making its product at bigger scales: “There was this 200-year-old invention that we had been inventing round.”
So the crew went looking and found that there are different pathways to the chemical bonds that give concrete made with Portland cement its power. Elegant’s materials takes one in every of these different routes: quite than alite, it makes use of lime and reactive silicates to react with water to type the ultimate materials.
The selection of cement chemistry may seem to be a minor quibble. However in a high-stakes business like development, it might be a key deciding issue during which startups win massive contracts and partnerships, and which fizzle out. “Persons are, I believe, rightfully skeptical of a brand new cement,” Ellis says, earlier than stopping herself: “Effectively, it’s and it isn’t a brand new cement.”
Ellis maintains that Elegant’s materials is as sturdy and sturdy as Portland cement, if no more so. However there’s an opportunity that builders will probably be hesitant, at the least initially, to maneuver away from the fabric they already know, says Local weather Crucial’s Lalit.
One of many main challenges forward for Elegant is making its materials on the large scales required for giant constructing initiatives. Trendy cement amenities can usually produce over 1,000,000 tons of cement every year, whereas Elegant’s pilot could make about 100 tons per 12 months. It’s principally “a cement plant for ants,” Ellis says.
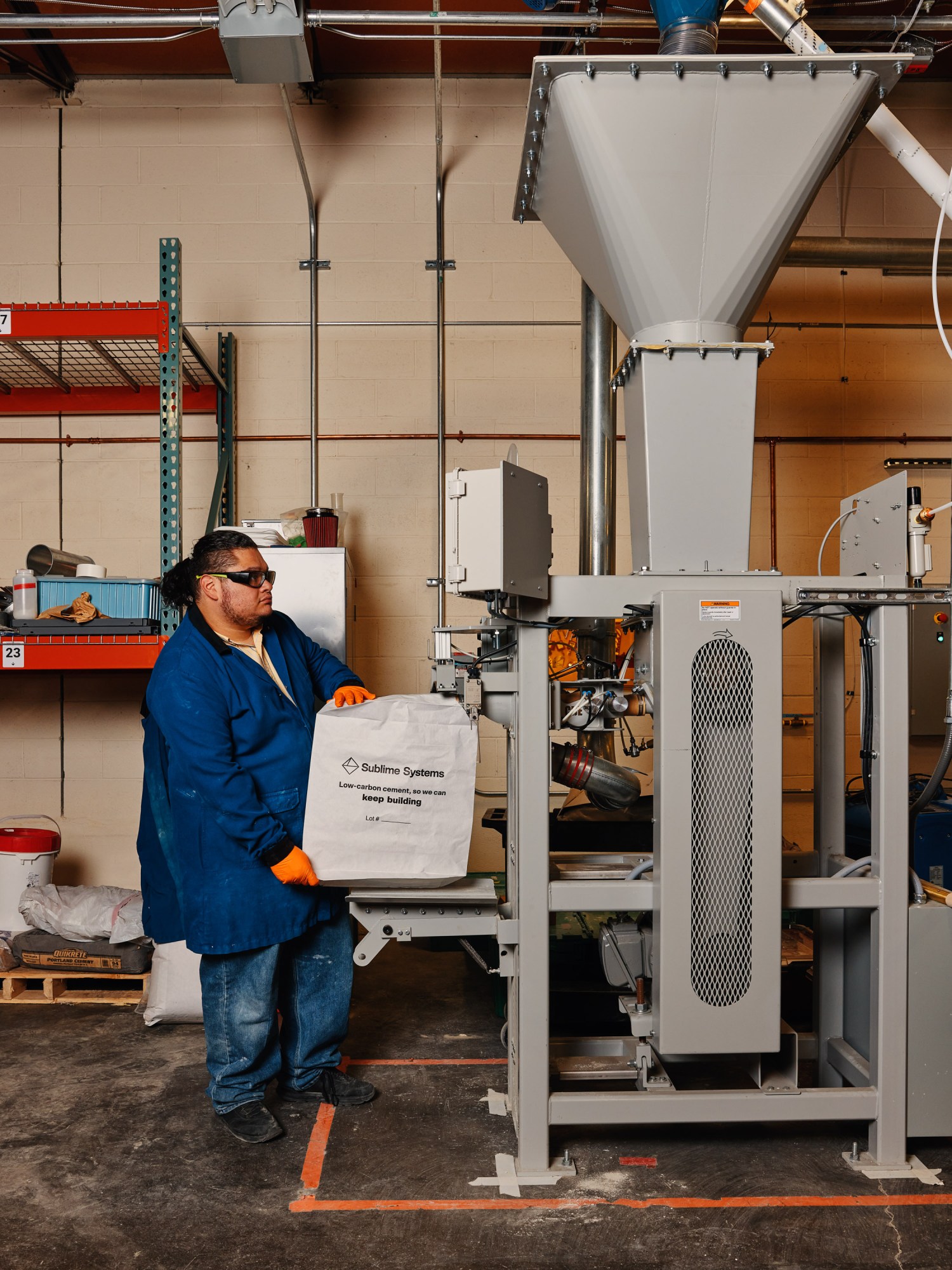
Elegant has its sights set on scaling, and shortly. The following stage for the startup is an illustration industrial facility producing tens of hundreds of tons of fabric every year, which ought to come on-line in early 2026. “That’s the scale the place you’re now not invisible to the cement world,” Ellis says.
After that will come a full-scale industrial plant able to the million-ton annual manufacturing capability that’s typical of the business. The corporate continues to be figuring out the place to construct that, although the hope is to get it working round 2028.
Elegant’s founding duo isn’t naïve in regards to the challenges forward. “A cement startup might be one of the tough ones you’ll be able to think about,” Ellis says. “Not solely is it technically tough, however it’s very capital intensive. It’s large. And it’s not attractive … everyone makes use of and owns cement, however they don’t see it.”
However fixing this invisible downside might remodel the world round us. Cement scaffolds our society, and efforts to alter it—regardless of the great challenges they face—are essential to cleansing up the way forward for development.