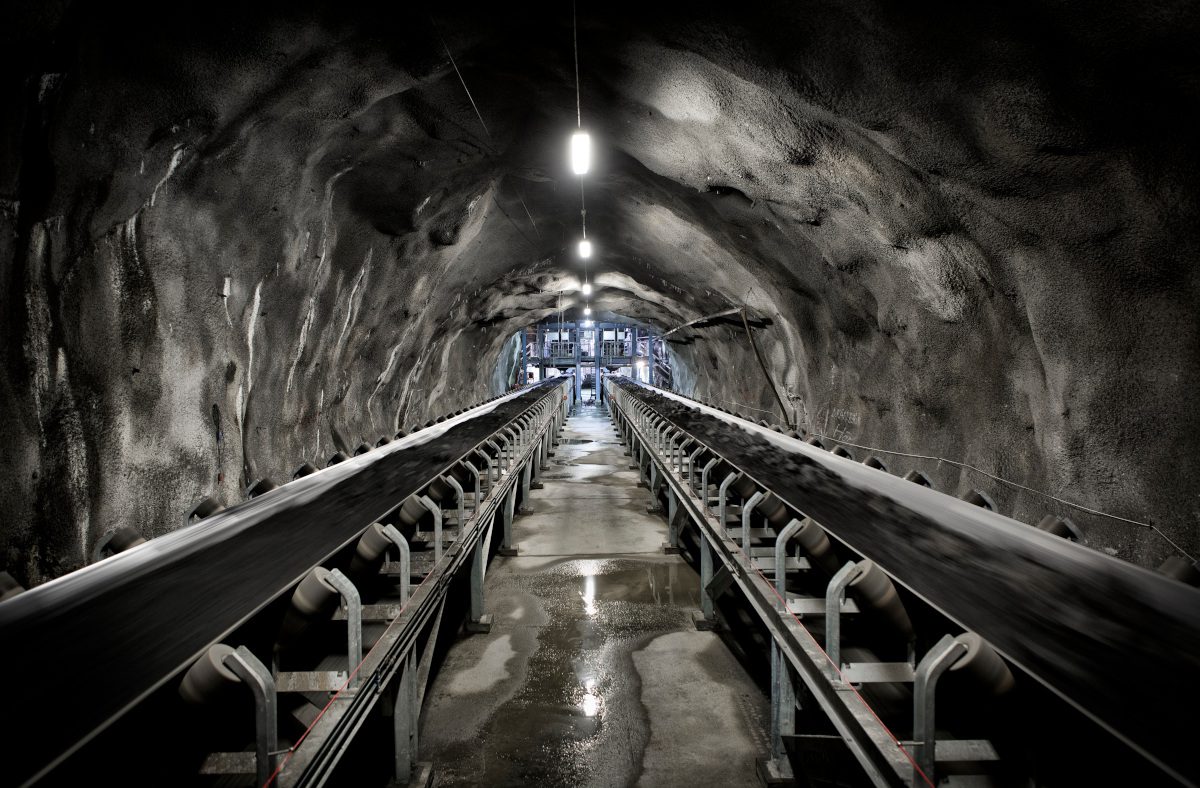
LKAB has awarded ABB a contract to put in two ABB Gearless Conveyor Drives (GCDs) on the present conveyor belt system at its Malmberget mine close to Gällivare, Norrbotten County, Lapland, essentially the most northern province in Sweden.
The prevailing setup already carries as much as 15 million tons of iron ore yearly, utilizing a 2,800kW wound rotor induction motor (WRIM) with gearbox to drive the conveyor. It is going to be changed with ABB’s newest GCD know-how, two 1,600kW fashions with everlasting magnet motors (PMM), to allow a rise in annual manufacturing whereas lowering vitality consumption per ton.
ABB’s set up engineers and mission administration workforce face the problem of working in a good area at round 1,250 meters underground to take away the massive tools and substitute it with the brand new items. As soon as the improve is full in 2025, LKAB will be capable of obtain total vitality financial savings of between 6 and 10 %, which can translate to appreciable OPEX financial savings per yr.
ABB GCDs have a motor energy of between 0.2MW and 8MW, eradicating the necessity for a gearbox and thereby reducing upkeep prices whereas enhancing total reliability and resulting in larger uptime. A singular ABB innovation, they’re recognized to be essentially the most energy-efficient conveyor drive resolution.
“We’re managing the most important iron ore mines in Europe the place productiveness should stay excessive whereas vitality effectivity will increase,” stated Pär Sundqvist, Engineer and Venture Proprietor, LKAB. “This vital improve will enhance the throughput on the conveyor and assist us to fulfill our vitality targets. ABB’s know-how will even scale back each OPEX per ton and ongoing lifecycle prices.”
“The brand new ABB tools will permit for an improved working setting within the mine – cleaner and safer,” stated Ulf Richter, Product Supervisor Conveyor Options, ABB. “Gearless Conveyor Drives are recognized to be essentially the most energy-efficient resolution for conveyors, enabling dependable transportation of ore. The improve additionally means diminished noise and warmth within the conveyor drive space.”
The GCD’s PMM are straight coupled to the present conveyor’s drive pulley and may tailored to fulfill the actual calls for of this underground set up. The principle benefits are vitality financial savings, well being and security enhancements, diminished upkeep prices and regular, strong manufacturing attributable to greater reliability.
ABB was awarded the mission contract within the third quarter of 2023 and the set up will happen throughout scheduled upkeep stops with the ultimate commissioning due in August 2025.