Manufacturing facility constructed houses should not a brand new concept. Way back to the tip of World Conflict II, households have been shopping for and residing in houses that have been moved onto tons in pre-assembled style. Normally known as “cell houses,” their mobility was questionable as soon as they have been positioned on a web site, in a improvement of comparable houses euphemistically known as a Park, or on a rural lot. The one cell half is the transport to the setup location. Because the idea grew, concrete foundations have been laid, making the mobility issue moot.
Manufactured housing was, at first, a Wild West setting with minimal guidelines and even fewer laws. Then, in 1976, the Congress handed the Nationwide Manufactured Housing Building and Security Act, altering the business. The Act declared that each one manufactured houses must be construct utilizing powerful nationwide requirements. Since then, enhancements have been added to make sure security as development customary have been raised.
At the moment, modular housing has taken the place of cell houses within the terminology of actual property brokers. A modular home is created in a manufacturing facility, delivered in items to a web site, and assembled by a contractor. Facilities, home equipment, ornamental adjustments to make every unit personalised are added onsite. In the most effective state of affairs, the very fact of how the house was constructed is invisible as soon as the crew leaves, the constructing itself indistinguishable from hand constructed customized housing.
However architects, builders, and contractors have been sluggish to undertake modular buildings in some areas. Land costs, availability, and situation have been drawbacks. Estimating the price of a modular improvement has been an issue. A British agency with U.S. workplaces in Seattle, Modulous, is working to alter that through the use of know-how and a provide chain of companions.
The Modulous software program platform automates multifamily real-estate mission design, costing, and programming – which means builders, architects, and contractors can work out pricing and resolve whether or not a web site is viable in hours, not weeks. As well as, Modulous has developed a configurable Package of Elements, which is a set of proprietary sub-assembles that permits builders, architects, and contractors to construct modular houses with out a fastened manufacturing facility. The corporate’s end-to-end platform allows 50% quicker mission supply, 60% discount in embodied carbon, and 70% discount in development waste.
The outcomes are spectacular:
- Structure and design – Modulous’ software program generates optimized designs and massing for a web site and bases these on its bodily Package of Elements. This not solely ensures the technical feasibility of the design, but in addition gives correct prices and schedule, all accomplished in hours. Architects can keep away from spending weeks on speculative work, designing schemes that will prove to not be economically viable, and as a substitute current purchasers with a wide range of choices inside a day, upping their probabilities of profitable work whereas letting them give attention to extra productive duties.
- Building – Modulous’ Package of Elements allows basic contractors to ship multi-story condominium blocks with no upfront funding. As an alternative of requiring advanced and dear factories, Modulous’ established provide chain companions ship sub-assemblies to meeting amenities close to web site, rising margin, using native labor, and bettering working capital effectivity.
- Growth – The Modulous platform produces 3D visualizations and detailed value plans, and it’ll present builders a real-time evaluation of return-on-investment calculations, enabling them to shortly possibility websites and set up land values pushed by correct information.
Modulous’ provide chain companions have centered their collaboration on repeatedly decreasing the variety of parts required, much like the strategy beforehand taken by the automotive and aviation industries. By monitoring every of those parts, it will likely be potential to measure and calculate the correct carbon content material of a plan and guarantee using wholesome, non-toxic supplies.
Modulous has created a high-performance Package of Elements to standardize the unseen components of development. Every component of the equipment has a digital equal within the software program, guaranteeing value and procurement data is accessible upfront. The Package of Elements is manufactured inside a provide chain, eradicating the necessity for fastened factories, and permitting builders to make use of and upskill native labor to assemble the equipment into volumetric modules near the development web site.
Whereas standardization is a key component of the method, it doesn’t imply that the whole lot has to look the identical. Customary parts, like the fundamental construction, have distinctive components, corresponding to interchangeable variations for various wall panels, flooring, and finishes. You’ll be able to rearrange issues so long as they don’t break the manufacturing mannequin, emphasizing configurability over customization.
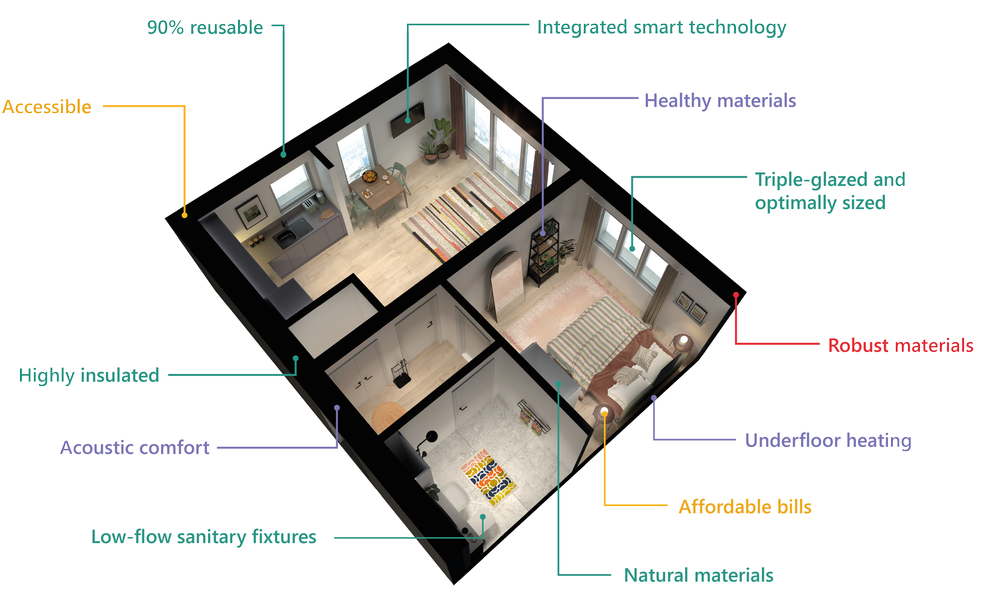
With the Package of Elements, the whole lot begins from a 3D digital illustration earlier than being manufactured bodily. This permits a developer to contemplate all of the issues that would usually intrude with each other within the design from the start. This could drastically diminish the variety of work change orders that always delay development.
The ideas have been acknowledged by many within the enterprise capital market, each within the U.Ok. and U.S., with funding. Modulous has raised $11.5 million of Collection A funding to additional develop its bodily and digital applied sciences. The funding is a uncommon instance of a tech agency rising its valuation as international markets slide – a testomony to rising curiosity in firms that assist decarbonize the true property and development industries.
Wish to tweet about this text? Use hashtags #development #sustainability #IoT #cloud #edge #futureofwork